材涂联动:国内唯一量产——苏州佩琦!
动力电池的采购费用已占整车成本的40%左右,动力电池的“绝缘阻燃&隔热密封”的安全性能——是影响消费者购车决策和汽车品牌美誉度的重要因素,目前各大主机厂已开始重点关注黑箱件动力电池,对动力电池电芯、液冷板、PACK盖板、汇流排的绝缘、阻燃等高性能涂层已开始投入大量人力、物力重点研究和开发。
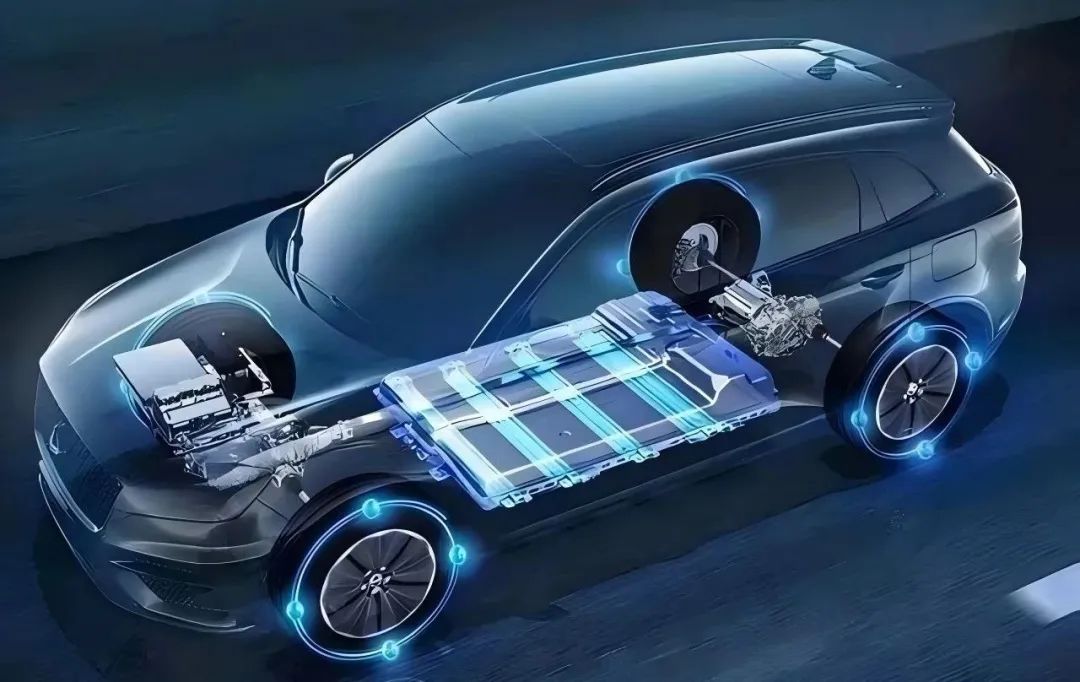
UV蓝光绝缘层有什么优势?
以BMW、CATL、Volvo、中创新航、国轩高科等新能源企业,已经开始转向一种全新的UV绝缘涂层方案,由此引发动力电池绝缘方案的新一轮升级。
小编通过对公开资料的整理比对,发现该UV蓝光绝缘层其实跟女士做美甲照灯的原理,有异曲同工之妙,在蓝紫色UV光源下,数秒照射,即可形成性能优异的绝缘涂层。
为了更好理解和记忆,小编把新一代UV蓝光绝缘层(UV blue insulating layer),简称为:UV蓝光绝缘层。
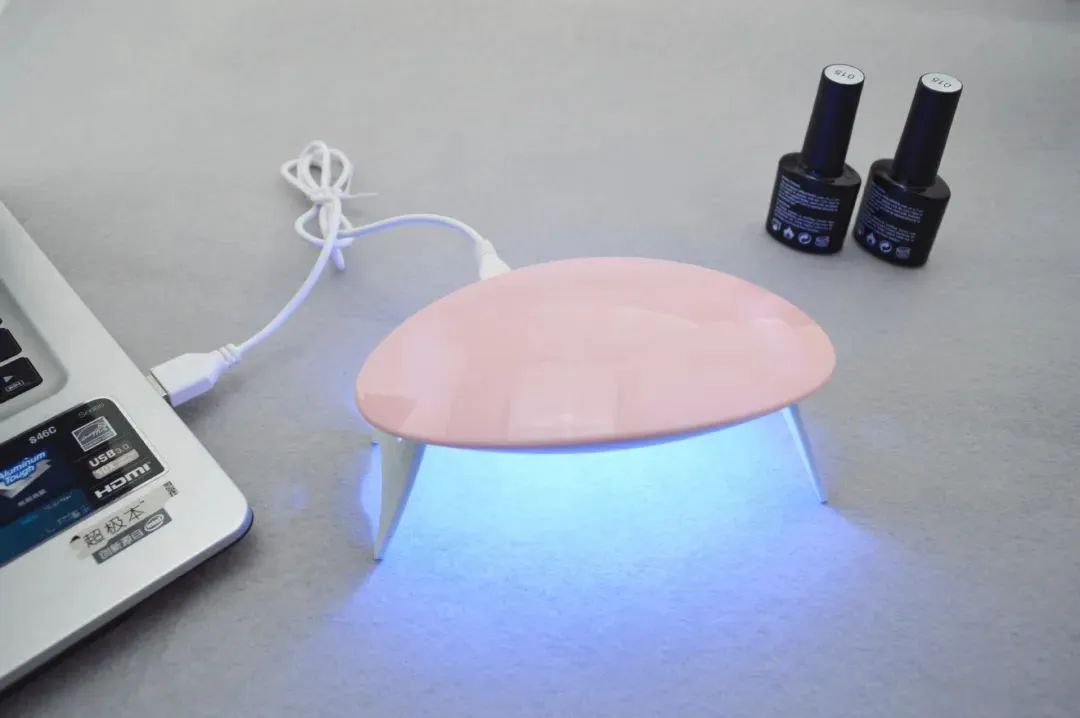
UV蓝光绝缘层——五大优势:
1、无VOCs,无废水,不需环评;
2、与电芯生产线无缝链接,不需喷涂车间;
3、高绝缘、 高剪切力,安全可靠;
4、全球36条量产线,55 ppm,高直通率 ;
5、材料、设备持续优化,未来接近PET蓝膜成本。
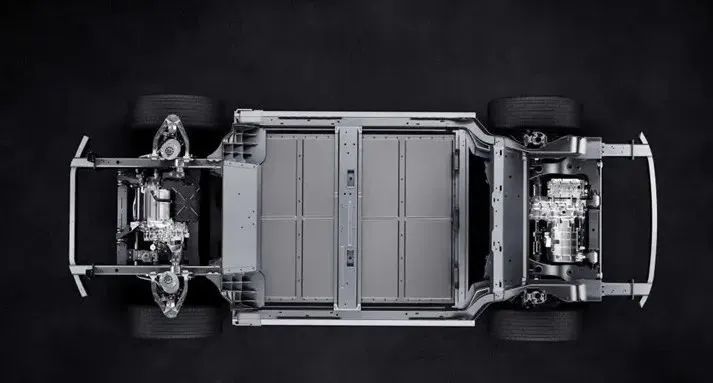
UV蓝光绝缘层制造线已完全融入电芯制造线,完全类似电子产品的生产线,快速高效,无需环评、无而单独建造涂层车间,主要特点如下:
工艺重大变化:在电芯壳体装入正负极材料后,然后激光焊接,在电池生产线无缝链接UV蓝光绝缘层生产设备;
效率更高:UV蓝光绝缘层目前已达到1.2s喷涂一个电芯盒体;
智能化:上下料、前处理、在线质量检测、缺陷修复都可全部自动化完成。

图1:电芯UV蓝光绝缘层工艺图

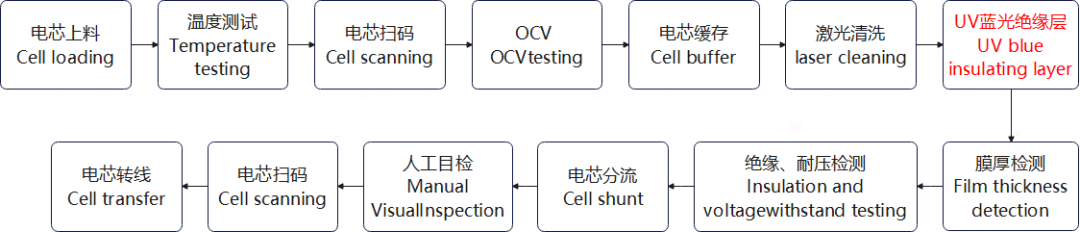
图2:UV蓝光绝缘层无缝接入——电芯生产线的工艺布局图
UV蓝光绝缘层可实现全自动产线,快速将产品完成喷涂及固化,工艺简捷,综合效率较高。

▲ UV蓝光绝缘层典型技术参数
动力电池“电芯”——“5种”绝缘工艺及成本对比
其中,PET蓝膜、粉末涂装、UV蓝光绝缘层、3种工艺已在应用量产。
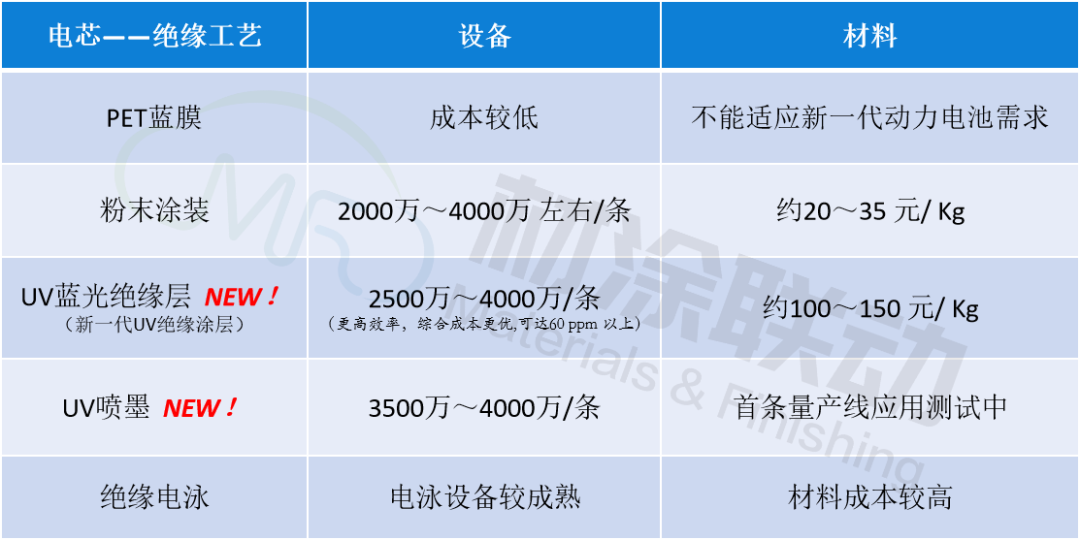
UV蓝光绝缘层:材料、设备厂家有哪些?
根据当前行业动态和技术路线划分,锂电池用UV蓝光绝缘层的主流材料厂家具体如下:
国际品牌
1、Lankwitzer蓝威
-
全球首个商用电池单元UV蓝光绝缘层厂商,主导产品EvoProtect455 UV系列,抗压强度>6KVDC,绝缘电阻>10GQ 。
-
累计为4.5亿颗电池单元提供绝缘涂层抗压强度>6KVDC,绝缘电阻>10GQ 。
2、宣伟(Sherwin-Williams)
-
UV蓝光绝缘层介电强度>3500V/100ym,通过UL94-V0阻燃认证,适配800V高压系统。卓越的耐环境性能,通过双85测试。
-
宣伟UV蓝光绝缘层有着优异的附着力提供全面保护,优异的耐电解液性能和超高的涂装效率。
3、立邦
-
推出单次喷涂50微米厚度的UV蓝光绝缘层,无需高温烘烤,降低能耗,广泛应用于木器、电池等领域。
-
采用自主研发的树脂材料和优选颜填料,实现了无 VOC 排放,具有极佳的附着力、柔韧性、高硬度、耐磨损性,能适应电池充放电过程中的膨胀和收缩,有效杜绝电流泄漏。
4、PPG
-
固化速度快,通常只需 1 秒钟左右或更短时间即可固化,可进行快速连续化作业,大幅提高生产效率。
5、派克洛德(Parker Lord)
-
Sipiol UV蓝光绝缘层采用紫外线固化技术,剪切强度>10Mpa,耐电解液腐蚀性能优异,通过多项绝缘测试。
自主品牌
6、苏州佩琦
-
自主品牌国产唯一量产——UV蓝光绝缘层的材料厂家,自主研发UVCuringPKP®方案,实现一喷一固,剪切强度>12Mpa(蓝膜的4倍),良率>99%,目前已装配多款车型;
-
已应用于方形电池、圆柱电池等,综合成本降低60%,材料可回收利用。
7、珠海展辰
-
展辰UV蓝光绝缘层,在高温下仍能保持极强的稳定性,相比常规UV蓝光绝缘层,下线堆叠过程中长时间高温也不易黄变,绝缘性能优异。
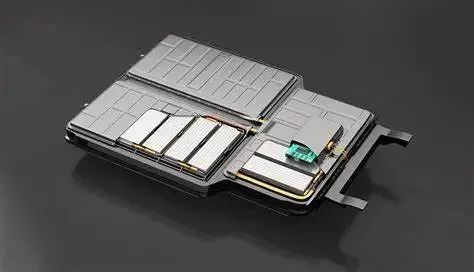
锂电池用UV蓝光绝缘层的主流设备厂家具体如下:
1、斯德拉马
-
斯德拉马是UV蓝光绝缘层设备的领先者,是全球唯一一家可以提供电芯整线解决方案并且有丰富量产经验的设备商。
2、斯德姆
-
UV蓝光绝缘层设备全球领先技术,已完成数个UV蓝光绝缘层设备的应用落地,智能化程度较高,生产节拍可达60ppm,稳定量产。
3、杜尔
-
在UV蓝光绝缘层涂装中,可高效地使用UV蓝光绝缘层,减少浪费和对环境的影响,且换色时的低损耗能提高生产效率,适用于需要频繁换色的UV蓝光绝缘层生产线。
4、中汽工程
-
中汽工程可实现UV蓝光绝缘层全自动产线,具备无VOCs挥发物、不含溶剂、绝缘性良好、附着力强、可燃性低以及固化后耐久性高等特征,可快速完成产品的喷涂及固化。
5、长虹
-
自主研发的UV蓝光绝缘层产线节拍为 50jpm,线速 375mm/s(可调整),可实现锂电池 OCV&ACR 自动检测、分选和前处理,外壳绝缘涂层的自动喷涂、固化、质量检测。
6、伟通科技
-
伟通科技把在车灯UV涂层生产线一直领先的30余年的专业经验,结合电芯绝缘的不同要求,实现了的智能化UV蓝光绝缘层硬化设备,结合领先的UV材料回收技术,对生产产品进行自动调整、控制和监测,实现无人化全自动生产。
7、加杰
-
加杰把在汽车内饰UV涂层的先进领先技术,结合电芯绝缘层的需求,整合了自动滑撬输送系统、自主研发的工装系统,能为UV蓝光绝缘层生产线提供稳定、高效的输送,确保工件在涂装过程中的精准定位和传输,有助于提高UV蓝光绝缘层的质量和一致性。
为什么PET蓝膜面临出局?
● 随着新一代动力电池结构:CTP、CTB、CTC的发展和应用;
● 动力电池800V高压快充技术的应用;
● GB 38031《电动汽车用动力蓄电池安全要求》标准的升级,明确要求热扩散不起火、不爆炸;
● PET蓝膜——无法满足:大尺寸刀片电池电芯&储能电芯,一次通过率的稳定制造要求;
对电芯及电池PACK系统的涂层绝缘阻燃、隔热密封的安全提出了较高要求。
具体来看,新一代动力电池结构的变化,电芯可直接粘接在PACK盖板或车身底盘,这就直接导致电芯粘接的剪切力度要求提升至9~15Mpa。
但蓝膜的PSA背胶粘接性能十分有限,基本处于0.5~2Mpa的水平;另一方面蓝膜的PET基材属于低表面能材料,这就让结构胶在其上产生的粘接强度也只能达到2.0~3.5MPa的中低水平。

因此,当电池组受到外力冲击,很可能使结构胶发生界面破坏从蓝膜上脱落;甚至蓝膜的PSA背胶发生内聚破坏直接让蓝膜从电芯外壳上脱落剥离。

另外,随着工作电压与能量密度的提升,让电芯之间产生电弧或者绝缘击穿的概率大幅增加。如传统蓝膜耐击穿电压最高仅支持2500V,而800V电压平台要求耐击穿电压3000~4000V,且强制性国家标准《电动汽车用动力蓄电池安全要求》(征求意见稿)中要求:电池包及系统绝缘电阻值≥ 100 Ω/V,且PET蓝膜——无法满足:大尺寸刀片电池电芯&储能电芯,一次通过率的稳定制造要求。综合来看,蓝膜方案已无法进一步满足技术需求。
UV蓝光绝缘层有哪些优势?动力电池绝缘阻燃发展趋势是什么?
关于动力&储能电芯 UV蓝光绝缘层的优势、发展趋势等,将在2025年4月23~25日,在中国新能源之都——江苏常州举办的第7届 MF高颜值、高性能涂层峰会有详细的技术和应用介绍。
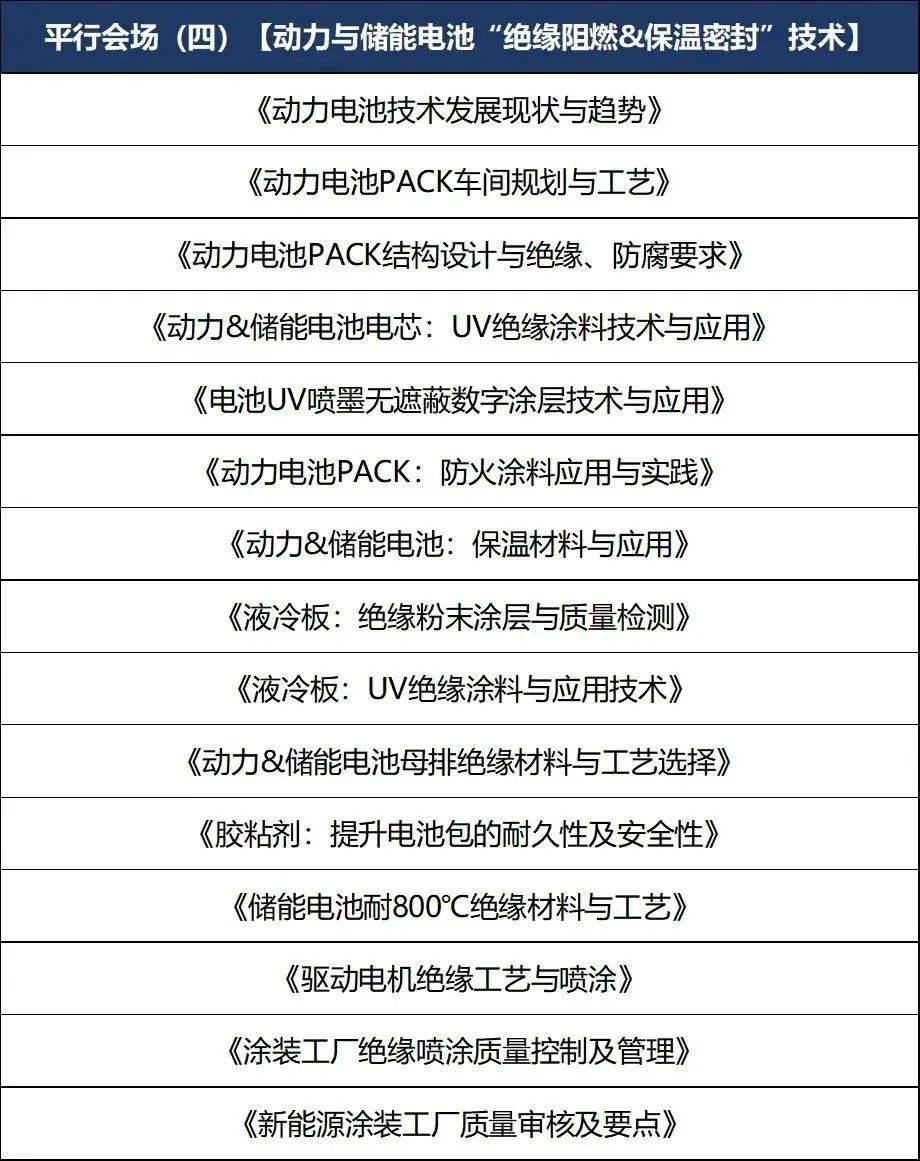